Navigating the intricate world of electrical connections can be daunting. From choosing the right connector kit for a specific application to understanding the nuances of installation and troubleshooting, meticulous planning and execution are paramount. This comprehensive guide dissects the essential aspects of electrical connector kits, equipping you with the knowledge to make informed decisions and ensure reliable electrical systems.
This guide covers everything from the fundamental principles of electrical connector kits to advanced considerations such as industry-specific applications and sustainability. It details various connector types, materials, and installation techniques, while also outlining crucial safety protocols. The analysis also includes a breakdown of cost factors and the environmental impact of different connector kits.
Introduction to Electrical Connector Kits
Electrical connector kits are pre-assembled packages of various electrical connection components, designed to simplify and expedite the process of wiring and interconnecting electrical devices. They are crucial for a wide range of applications, from residential wiring to complex industrial machinery. These kits streamline the assembly process by providing all the necessary parts in a single convenient package.
Types of Electrical Connector Kits
Electrical connector kits encompass a diverse range of components, catering to various needs and applications. These kits commonly include wire connectors, terminal blocks, and insulated sleeves. Wire connectors, often crimp or solder style, facilitate the connection of wires. Terminal blocks offer a structured way to connect multiple wires or cables, commonly used in panel mounting applications. Insulated sleeves provide protection and insulation at the connection points.
Furthermore, specialized kits are available for specific applications, such as high-voltage connections or high-temperature environments.
Common Applications in Various Industries
Electrical connector kits are fundamental in diverse industries. In the automotive industry, they facilitate the connection of various electrical components, ensuring proper functioning of the vehicle’s systems. The industrial sector leverages these kits to connect machinery, sensors, and control systems, enabling efficient automation and control. Residential applications also rely on connector kits for safe and reliable wiring in homes and buildings.
Specialized kits are available for data centers, ensuring robust connections for high-speed data transmission.
Key Components of a Typical Electrical Connector Kit
Component | Function |
---|---|
Wire Connectors | These connectors facilitate the secure joining of wires, ensuring reliable electrical contact and preventing unwanted current leakage. |
Terminal Blocks | These provide a structured method for connecting multiple wires or cables, often mounted on panels. They offer a standardized way to connect and organize various circuits. |
Insulated Sleeves | These sleeves are crucial for providing electrical insulation and protection at the connection points, preventing short circuits and ensuring safety. |
Screws and Fasteners | These are used to secure the connections and maintain the structural integrity of the assembled circuit. |
Insulation Tape/Heat Shrink Tubing | These materials are used to provide additional insulation and enhance the overall protection of the connection, preventing moisture ingress and damage. |
Crimping Tools/Soldering Tools | Specialized tools are needed to properly assemble certain types of connectors. |
Choosing the Right Connector Kit
Selecting the appropriate electrical connector kit is critical for ensuring safe, reliable, and efficient connections. A poorly chosen kit can lead to costly repairs, downtime, and even safety hazards. Careful consideration of various factors, including voltage and amperage ratings, material properties, and safety features, is essential for a successful installation.Choosing the correct connector kit hinges on several key factors that directly influence performance and longevity.
Understanding these parameters is paramount to avoiding costly mistakes and ensuring a secure connection.
Voltage and Amperage Ratings
Electrical connectors are rated for specific voltage and amperage limits. Exceeding these limits can lead to overheating, potential fire hazards, and component failure. Carefully matching the connector kit’s ratings to the electrical system’s specifications is vital. For example, a 120V circuit requires different connectors than a 480V industrial system. Consulting the manufacturer’s specifications is critical to prevent any overloads.
Material Properties
The material used in electrical connectors significantly impacts their performance and longevity. Common materials include copper, brass, and aluminum. Copper is known for its excellent conductivity and corrosion resistance, making it a popular choice for high-current applications. Brass offers a good balance of conductivity and cost-effectiveness, often suitable for lower-current scenarios. Aluminum, while lighter and less expensive than copper, has lower conductivity and is more susceptible to corrosion.
The selection depends on the specific application requirements.
Safety Features
Safety features in connector kits are paramount. Insulation, grounding provisions, and strain reliefs are critical for preventing electrical shocks, short circuits, and other hazards. Ensuring that the chosen kit incorporates these features is a fundamental safety consideration. For example, a kit with a robust strain relief mechanism will prevent wire damage and maintain a secure connection.
Comparison of Connector Types
Different connector types offer varying performance characteristics, including speed of installation, reliability, and cost. A comparative analysis helps in making informed decisions.
Connector Type | Speed | Reliability | Cost |
---|---|---|---|
Crimp Connectors | Medium | High | Low |
Screw Terminals | Low | Medium | Very Low |
Wire Connectors | High | Medium | Medium |
The table above provides a general overview. Specific performance characteristics may vary based on the manufacturer and the specific connector type. For instance, the speed of installation can vary based on the complexity of the connections and the skill level of the installer. Reliability is also affected by factors like the quality of the materials and the manufacturing process.
Cost varies significantly depending on the type, quantity, and complexity of the connector.
Installation and Usage Procedures
Proper installation of electrical connector kits is crucial for ensuring safe and reliable electrical connections. Incorrect procedures can lead to short circuits, fire hazards, and even personal injury. Adherence to the manufacturer’s instructions and established safety protocols is paramount. This section details the steps involved, emphasizes proper techniques, and highlights potential pitfalls.Electrical connections, though seemingly simple, demand precision and attention to detail.
Careless handling can compromise the integrity of the entire system, resulting in malfunction or even catastrophic failure. This section will guide users through the process, equipping them with the knowledge and techniques to achieve secure and safe electrical connections.
Step-by-Step Installation Procedure
Following a methodical approach during installation is critical. A standardized procedure minimizes the risk of error and ensures a robust connection. The steps Artikeld below are general guidelines; specific instructions may vary based on the type of connector kit.
- Verify Component Compatibility: Ensure that the wires and connectors are compatible. Mismatched components can lead to poor electrical contact and eventual failure. Consult the connector kit’s specifications for compatibility details.
- Prepare the Wires: Carefully strip the insulation from the ends of the wires to expose the conductor. The correct stripping length is crucial for proper insertion into the connector. Stripping too much or too little can hinder connection and cause damage.
- Insert Wires into Connectors: Align the wire ends with the connector’s terminals and insert them firmly. The proper insertion depth ensures reliable contact. Incorrect insertion can lead to loose connections and potential overheating.
- Secure the Connectors: Secure the connector according to the manufacturer’s instructions. This may involve tightening screws, crimping terminals, or other methods. Improper tightening can result in loose connections, while excessive tightening can damage the connector.
- Test the Connection: Perform a visual inspection of the connections and verify the electrical continuity. A multimeter can be used to check for proper conductivity. This step is vital for identifying potential issues before further use.
Connecting Wires to Connectors
The technique used to connect wires to connectors significantly impacts the longevity and safety of the connection. Applying the right technique is essential for optimal electrical conductivity and minimal risk.
- Using Wire Strippers: Use appropriate wire strippers to ensure a clean cut of the insulation. This prevents damage to the wire and facilitates proper insertion into the connector.
- Correct Insertion Depth: Insert the wires into the connector terminals to the correct depth. This ensures adequate contact with the connector’s metal surface, providing optimal conductivity.
- Tightening Screws (if applicable): Tighten the screws or fasteners securing the connector according to the manufacturer’s recommendations. Over-tightening can damage the connector, while under-tightening can result in a loose connection.
Common Installation Mistakes and Consequences
Errors in installation can have detrimental effects. Avoiding these pitfalls is essential for preventing hazards and ensuring the safety of the electrical system.
- Improper Wire Stripping: Insufficient or excessive wire stripping can lead to poor electrical contact, increasing the risk of overheating and potential fires.
- Loose Connections: Loose connections are a significant concern. They can cause intermittent operation, overheating, and ultimately, failure of the entire system.
- Incorrect Connector Selection: Using an unsuitable connector for the application can compromise the strength of the electrical connection. This can lead to short circuits or failure of the equipment.
Safety Precautions
Working with electrical connector kits necessitates adherence to strict safety precautions. These precautions are designed to mitigate the risk of accidents and ensure a safe working environment.
Safety Precautions | Explanation |
---|---|
Wear appropriate safety gear | Protective gloves, safety glasses, and appropriate footwear are vital for preventing electrical shocks and physical injuries. |
Ensure proper grounding | Proper grounding is essential to prevent electrical shocks and ensure the safety of the system. |
Work in a well-ventilated area | Adequate ventilation minimizes the risk of exposure to harmful fumes or gases. |
Disconnect power supply | Before any installation or maintenance, ensure the power supply to the electrical system is disconnected to prevent electrical shocks. |
Follow manufacturer instructions | Adhering to manufacturer instructions minimizes the risk of errors and ensures optimal performance. |
Troubleshooting Electrical Connector Kits
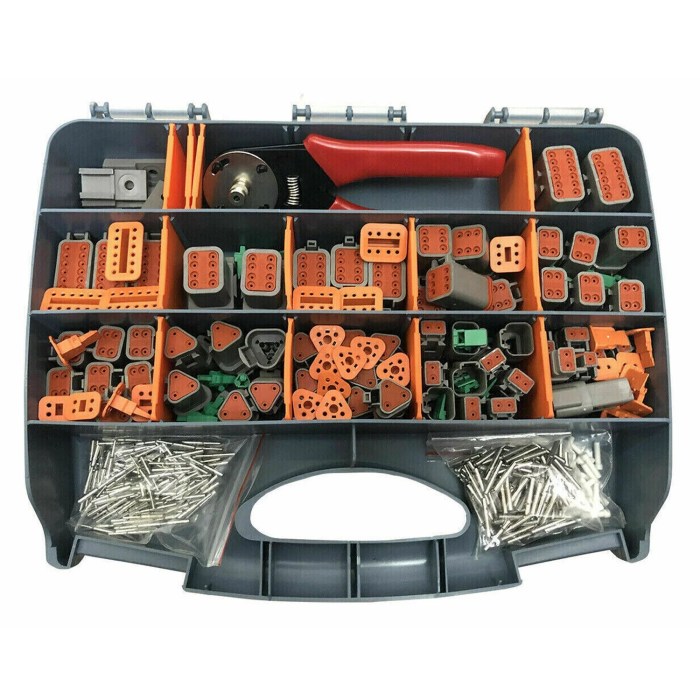
Electrical connector kits, while designed for ease of use, can sometimes present challenges during installation or operation. Understanding potential issues and their diagnoses is crucial for maintaining system integrity and preventing costly downtime. Proper troubleshooting ensures that the kit functions as intended, avoiding unforeseen problems and improving overall system reliability.
Potential Issues with Electrical Connector Kits
Electrical connector kits, like any complex system, can encounter various issues. These can range from simple misconnections to more complex problems involving material degradation or improper installation procedures. Identifying these issues early is key to preventing larger, more costly problems down the line. A methodical approach to diagnosis is essential for efficient troubleshooting.
Diagnosing Problems with a Connector Kit
Diagnosing problems with a connector kit involves a systematic process. First, carefully inspect the connector kit for any visible damage or signs of improper installation. This includes checking for loose connections, bent pins, or signs of overheating. Next, verify the proper wiring configuration against the manufacturer’s specifications. If the wiring is correct and the physical inspection yields no apparent issues, further diagnostics using appropriate measuring tools are necessary.
This could involve using a multimeter to check for continuity and voltage readings. If the issue persists, a review of the installation procedures, considering any deviations from the recommended practices, is also crucial.
Troubleshooting Tips for Common Connector Kit Malfunctions
Effective troubleshooting involves a combination of methodical checks and specific techniques. Carefully reviewing the installation instructions is crucial. These documents typically provide guidance on identifying potential problems and steps for resolving them. Using appropriate diagnostic tools like multimeters can assist in identifying circuit faults and pinpointing the specific location of the issue. If the issue persists, consulting with a qualified technician or the manufacturer’s support team is recommended.
These resources often provide specialized expertise in handling complex troubleshooting scenarios.
Common Connector Kit Problems and Solutions
Problem | Possible Cause | Solution |
---|---|---|
Connector won’t connect | Loose or bent pins, incorrect wiring, damaged connectors, or incompatible parts. | Check for loose pins and ensure they are properly seated. Verify the wiring configuration against the schematic. Inspect the connectors for damage and replace if necessary. Ensure the parts are compatible with the connector kit. |
High resistance reading | Oxidized contacts, poor connections, or damaged wires. | Clean the contacts with a suitable contact cleaner. Tighten any loose connections. Inspect and replace damaged wires. |
Short circuit | Improper wiring, damaged insulation, or metal-to-metal contact. | Verify the wiring configuration against the schematic. Check for damaged insulation. Isolate the short circuit by carefully inspecting the wiring and connections. |
Connector overheating | Excessive current flow, loose connections, or poor contact. | Ensure the correct amperage rating for the connector is being used. Tighten any loose connections. Verify the wiring configuration and ensure appropriate thermal dissipation. |
Maintenance and Safety Considerations
Proper maintenance and adherence to safety protocols are crucial for the longevity and safe operation of electrical connector kits. Neglecting these aspects can lead to malfunctions, potential hazards, and costly repairs. This section Artikels the essential procedures for maintaining and utilizing electrical connector kits safely.Regular inspection and cleaning, combined with appropriate storage practices, can significantly extend the lifespan of the connectors and associated components.
Following safety protocols minimizes the risk of electrical shock, fire, and other potential accidents.
Importance of Regular Maintenance
Regular maintenance is essential for preventing corrosion, wear, and tear on electrical connectors. Over time, environmental factors such as moisture, dust, and temperature fluctuations can degrade the components’ performance. This deterioration can lead to intermittent connections, reduced conductivity, and even complete failure. Routine cleaning and inspection can identify potential problems before they escalate into major issues. By addressing minor issues promptly, the overall reliability and operational lifespan of the electrical connector kit are significantly improved.
Proper Storage Procedures
Proper storage is crucial to preserving the integrity of electrical connectors and minimizing the risk of damage. Connectors should be stored in a cool, dry, and well-ventilated environment to prevent moisture buildup and corrosion. They should be protected from direct sunlight and extreme temperatures. Using appropriate packaging and organizing components logically within designated storage spaces is essential.
This organized storage approach ensures easy access to specific components when needed and prevents potential misplacement.
Safety Protocols for Handling Electrical Connector Kits
Adhering to safety protocols is paramount when working with electrical connector kits. Before any installation or maintenance task, always disconnect the power source to avoid electrical shock. Ensure proper grounding to prevent accidental electrical currents. Use insulated tools and appropriate personal protective equipment (PPE), such as gloves and eye protection, to prevent accidental injuries. Adhering to these safety protocols significantly reduces the risk of harm.
Training on proper handling techniques is highly recommended.
Tools and Equipment for Maintenance
Maintaining electrical connector kits effectively requires a selection of tools and equipment. A basic toolkit should include:
- Insulated screwdrivers of various sizes
- Wire strippers
- Crimping tools
- Needle-nose pliers
- Voltage testers
- Cleaning brushes
- Degreasing agents (for connectors exposed to high levels of grease or dirt)
The choice of tools will depend on the specific types of connectors within the kit. Using the correct tools is critical for both efficient maintenance and preventing damage to the connectors. Regular inspection and maintenance with the appropriate tools contribute significantly to the overall safety and reliability of the electrical system.
Different Types of Connections
Electrical connector kits offer diverse connection methods, each with unique strengths and weaknesses. Understanding these differences is crucial for selecting the appropriate kit for a specific application, ensuring reliable and efficient electrical systems. Choosing the right connection method impacts everything from installation time to long-term system integrity.
Crimp Connections
Crimp connections involve deforming a connector’s metal housing to create a secure electrical contact. This method is widely used due to its simplicity and speed. The contact pressure is precisely controlled by the crimping tool, ensuring a reliable connection.
Solder Connections
Solder connections involve melting solder to fuse metal conductors together. This method provides a robust and permanent connection, particularly suitable for high-current applications. However, the process requires specialized tools and training, adding to the complexity and potential for errors.
Screw Connections
Screw connections utilize screws to clamp the conductors between the connector’s terminals. This method is often chosen for its ease of assembly and adjustability. However, it may not be as durable as crimp or solder connections, particularly in environments with vibration or high temperatures.
Comparison Table
Connection Type | Advantages | Disadvantages | Typical Applications |
---|---|---|---|
Crimp | Fast, relatively simple, reliable under typical conditions, cost-effective for many applications. | Requires specific tools, potentially less durable in extreme environments. | Wiring in residential houses, low-voltage industrial control panels, automotive wiring. |
Solder | High-current carrying capacity, permanent connection, suitable for high-temperature applications. | Requires specialized training, potentially more time-consuming, higher risk of errors. | High-power electronics, sensitive circuits, applications requiring a very reliable connection. |
Screw | Simple, adjustable, widely available tools. | Less robust than crimp or solder, susceptible to loosening over time, not ideal for high-vibration environments. | Simple electrical panels, low-current connections, temporary wiring, some industrial applications with low-impact environments. |
Choosing the Right Connection Type
The selection of a specific connection type depends heavily on the specific application’s requirements. Factors such as the required current carrying capacity, environmental conditions, the desired level of reliability, and the availability of tools and expertise play a significant role in the decision-making process. Consider the potential for future maintenance or modifications when choosing. For example, a crimp connection might be suitable for a simple lighting circuit, while a solder connection might be necessary for a high-power electrical system.
Material and Construction
Electrical connector kits, crucial components in any electrical system, rely heavily on the quality and suitability of their materials. The longevity and reliability of these kits are directly linked to the chosen materials and their construction methods. Selecting appropriate materials is critical for ensuring safety, durability, and optimal performance.
Material Selection Considerations
The materials used in electrical connector kits are chosen based on a range of factors, including electrical conductivity, thermal stability, chemical resistance, and mechanical strength. These properties determine the connector’s ability to withstand various environmental conditions and stresses. The ideal material selection often involves a trade-off between these characteristics.
Plastic Materials
Plastic materials are commonly used in connector kits due to their lightweight nature, ease of molding, and relatively low cost. Polycarbonate, nylon, and various types of thermoplastic polymers are frequently employed. Polycarbonate, known for its high impact resistance and heat tolerance, is suitable for demanding applications. Nylon, with its excellent mechanical strength and dimensional stability, is commonly used in connectors that require higher stress resistance.
Metal Materials
Metal components, typically copper or brass, are essential for electrical conductivity. Copper’s high conductivity and corrosion resistance make it a preferred choice for conductors. Brass, an alloy of copper and zinc, often provides enhanced strength and corrosion resistance, making it suitable for applications exposed to harsh environments. The choice between copper and brass depends on the specific requirements of the application, such as the level of stress and expected environmental conditions.
Durability and Longevity
The durability and longevity of a connector kit are significantly influenced by the materials’ resistance to environmental factors like moisture, temperature fluctuations, and chemical exposure. For example, connectors exposed to high temperatures or corrosive environments necessitate materials with superior thermal and chemical resistance. A comprehensive material selection process is essential to ensure the connector kit maintains its functionality and safety throughout its lifespan.
Specific Materials in High-Demand Applications
High-demand applications often necessitate the use of specialized materials. In aerospace applications, connectors may incorporate high-strength, lightweight materials to meet stringent weight restrictions and ensure reliability in extreme conditions. Similarly, in marine environments, connectors need materials resistant to salt spray and moisture. For example, connectors used in automotive applications need materials that can withstand vibration, temperature changes, and potential impacts.
Choosing appropriate materials for each specific application is crucial for the long-term performance and reliability of the electrical system.
Industry Specific Applications
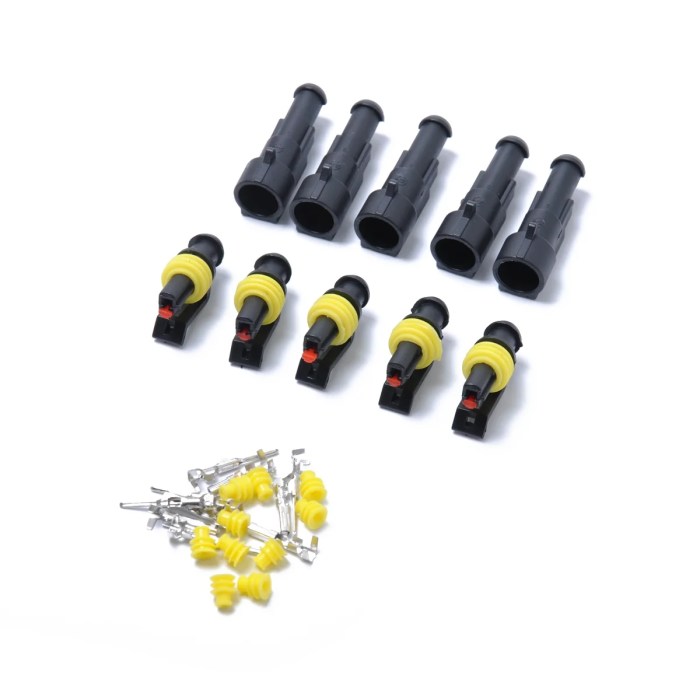
Electrical connector kits find widespread application across diverse industries, each demanding specific performance characteristics and environmental tolerances. The choice of connector type, material, and construction directly impacts reliability, safety, and overall system performance. Understanding these nuances is crucial for selecting the optimal connector kit for a given application.
Automotive Applications
Automotive electrical systems are complex, demanding connectors that withstand vibration, extreme temperatures, and harsh environmental conditions. Reliability is paramount, as failures can lead to safety hazards and costly repairs. Specific connector kits are designed to address these challenges.
- High-current applications: Automotive electrical systems often involve high-current loads, necessitating connectors capable of handling these demands without overheating or failing. Examples include starter motor connectors and battery connections. These connectors often incorporate robust metal housings and high-temperature resistant insulation to ensure longevity.
- Harsh Environments: Automotive connectors are subjected to vibration, moisture, and temperature fluctuations. Specialized sealing and shielding mechanisms are critical to prevent corrosion and maintain electrical integrity. For example, connectors used in engine compartments require robust waterproofing and vibration resistance to function reliably under demanding conditions.
- Miniaturization Trends: The trend toward vehicle electrification and advanced driver-assistance systems (ADAS) necessitates smaller, more compact connectors. High-density connectors are often used to minimize wiring harness bulk while maintaining high performance.
Aerospace Applications
Aerospace applications demand extreme reliability and durability, as failures can have severe consequences. Connectors must withstand the rigors of flight, including extreme temperatures, vibration, and pressure fluctuations.
- Environmental Challenges: Connectors in aerospace applications must withstand extreme temperatures, vacuum conditions, and potential exposure to harsh radiation. Materials selection and manufacturing processes are critical to ensure connector integrity.
- High-speed Data Transmission: Modern aerospace systems often require high-speed data transmission, demanding connectors that support these bandwidths. These connectors need to be meticulously designed to minimize signal degradation and interference. For instance, connectors used in aircraft communication systems need to be extremely reliable to avoid signal loss or distortion.
- Space Exploration: Space exploration applications require connectors that withstand the extreme conditions of space, including the vacuum of space and variations in temperature. Materials must be chosen for their resistance to extreme temperatures and radiation. Examples include connectors used in satellite systems and spacecraft components.
Industrial Applications
Industrial environments present a wide range of operating conditions, from high-temperature manufacturing processes to harsh chemical environments. Connector kits for industrial use must balance cost-effectiveness with high performance.
- Heavy-duty machinery: Industrial machinery often demands connectors that can withstand significant mechanical stress, vibration, and potential exposure to corrosive substances. Robust and durable connectors are crucial for ensuring reliable operation in these environments.
- Harsh chemical environments: In industrial settings involving chemical processes, connectors must resist corrosion and maintain electrical integrity. Corrosion-resistant materials are essential in such applications. For instance, connectors in chemical plants need to be made from materials resistant to specific chemicals.
- Automated systems: Automated systems in industrial settings require connectors that can withstand repeated insertions and removals. High-cycle connectors are specifically designed for these applications to ensure reliable connections over time.
Cost and Value Considerations
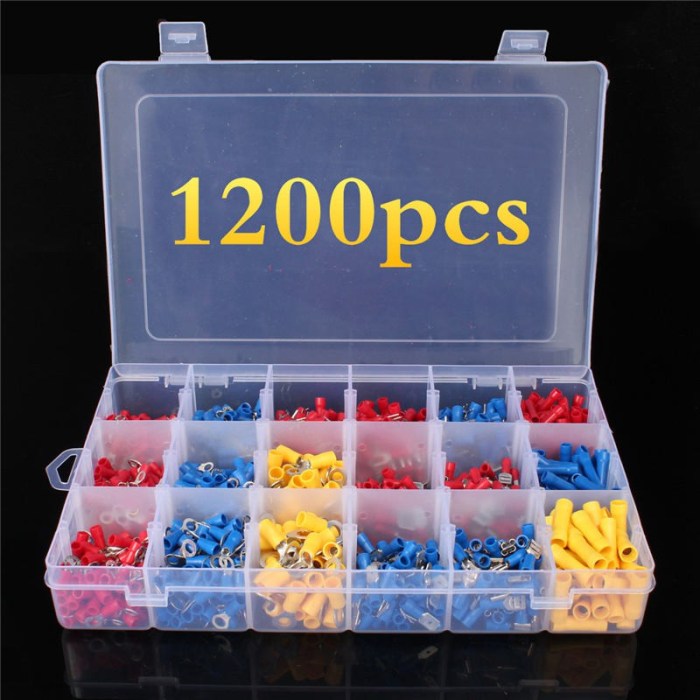
Electrical connector kits, while fundamental to any electrical infrastructure, present a spectrum of pricing and value propositions. Understanding the factors influencing cost and the relative value of different kits is crucial for informed procurement decisions. A comprehensive evaluation considers not only the initial price but also the long-term operational efficiency and potential for future upgrades.The cost of an electrical connector kit is multifaceted, encompassing material quality, manufacturing processes, design complexity, and the overall level of features included.
A kit boasting high-grade materials and sophisticated design features might command a higher initial price, but potentially offers greater durability, reliability, and reduced maintenance costs over the long term. Conversely, a basic kit, optimized for simplicity and low cost, might be suitable for less demanding applications but could compromise performance and longevity.
Factors Influencing Connector Kit Cost
Several factors significantly impact the price of an electrical connector kit. These include:
- Material Selection: Premium materials like high-grade copper or alloys with superior corrosion resistance drive up costs, but enhance the kit’s lifespan and reliability.
- Manufacturing Processes: Advanced manufacturing techniques, including automated assembly or specialized tooling, contribute to higher production costs.
- Design Complexity: Kits featuring intricate designs, multiple connection types, or enhanced safety features typically have a higher price tag.
- Included Components: The range and quality of components included, such as strain reliefs, insulation, and termination tools, influence the overall cost.
- Quantity Discounts: Purchasing in bulk often unlocks significant cost savings, making it an important factor for large-scale projects.
Comparing Costs of Different Connector Kits
Directly comparing costs across different connector kits necessitates a thorough evaluation of their specific features and applications. A simple, basic kit intended for residential wiring might cost significantly less than a high-performance industrial kit designed for demanding environments.
Kit Type | Typical Application | Approximate Cost (USD) | Value Proposition |
---|---|---|---|
Residential Wiring Kit | Household electrical installations | $50-$200 | Affordable and sufficient for standard residential applications |
Industrial Automation Kit | High-voltage, heavy-duty connections | $200-$1000+ | Robust, durable, and suitable for harsh environments; often includes specialized components. |
Specialty Connector Kit | Specific applications like aerospace or medical equipment | $500-$5000+ | Highly specialized features, premium materials, and rigorous testing |
Value Proposition of Different Connector Kits
The value proposition extends beyond the initial cost and encompasses the long-term benefits derived from using a particular kit. Factors such as reliability, durability, safety features, and ease of installation all contribute to the overall value.
- Reliability: Kits with robust materials and construction exhibit higher reliability, minimizing downtime and potential equipment failures.
- Durability: Superior materials and design contribute to a kit’s durability, reducing the need for frequent replacements and extending its operational lifespan.
- Safety Features: Kits equipped with safety features like insulation and strain reliefs ensure compliance with industry standards and safeguard personnel.
- Ease of Installation: Well-designed kits with clear instructions and compatible tools simplify installation procedures, reducing labor costs and project timelines.
Optimizing Connector Kit Value
Several strategies can optimize the value derived from an electrical connector kit:
- Strategic Procurement: Purchasing in bulk or through established distributors can often leverage discounts and expedite delivery.
- Material Considerations: Selecting high-quality materials might increase the initial cost, but could reduce long-term maintenance and replacement expenses.
- Component Selection: Choosing kits with appropriate features and components tailored to the specific application will optimize the value proposition.
- Skill Development: Investing in training for proper installation and maintenance procedures can maximize the operational efficiency and safety of the connector kit.
Environmental Impact and Sustainability
Electrical connector kits, while crucial for modern infrastructure and technology, have a potential environmental footprint. Minimizing this impact and adopting sustainable practices are increasingly important considerations for manufacturers and consumers alike. This section explores the environmental impact of these kits, examines the sustainable materials employed, and highlights examples of eco-friendly designs.The environmental impact of electrical connector kits stems primarily from the manufacturing process and the potential for e-waste.
Material sourcing, energy consumption during production, and the eventual disposal of these components all contribute to the overall ecological footprint. The push for sustainable solutions centers on reducing these impacts through material selection, optimized manufacturing, and improved end-of-life management.
Sustainable Materials in Connector Kits
A key element in mitigating the environmental impact is the selection of sustainable materials. Manufacturers are increasingly incorporating recycled and renewable resources in the production of connector kits. This shift allows for a reduced reliance on virgin materials, lowering the overall environmental footprint.
- Recycled polymers are often used in the housings and insulation components of connector kits, reducing the demand for newly extracted materials. This not only conserves natural resources but also minimizes the energy required for the production process.
- Bio-based plastics derived from plant sources are gaining traction as sustainable alternatives to traditional petroleum-based polymers. Their use significantly reduces reliance on fossil fuels and can offer comparable performance in electrical applications.
- Metals like aluminum and copper, essential for conductivity, are increasingly sourced through recycled streams. This reduces the environmental impact associated with mining and processing virgin materials.
Examples of Environmentally Friendly Connector Kits
Several manufacturers are pioneering designs that minimize environmental impact. These designs showcase the integration of sustainable materials and manufacturing processes.
- Some companies are designing connector kits with entirely recycled plastic housings. These kits demonstrate a commitment to circularity, reducing reliance on virgin materials.
- Others are utilizing bio-based plastics in conjunction with recycled metals, providing a balanced approach to material sustainability. This hybrid approach showcases a potential for a wide range of applications.
- Innovative designs often incorporate modular components, enabling easy disassembly and component reuse. This modular approach facilitates the circular economy by allowing for the recovery and repurposing of components during the product’s lifecycle.
Recycling Options for Electrical Connector Kits
Proper recycling is crucial for minimizing the environmental impact of e-waste. Many manufacturers are actively promoting and facilitating the recycling of their products.
- Dedicated recycling programs for electrical connector kits are available in some regions, providing a structured path for end-of-life components. These programs ensure responsible handling and recovery of valuable materials.
- Specific recycling facilities are equipped to handle the unique materials used in connector kits, ensuring the recovery of precious metals and other recyclable components. These facilities are often partnered with manufacturers to ensure appropriate recycling methods are employed.
- Materials like copper and aluminum are highly recyclable. The recovery of these metals from connector kits significantly reduces the need for new mining and processing, leading to a more sustainable resource cycle.
Ending Remarks
In conclusion, selecting and implementing the correct electrical connector kit is critical for both efficiency and safety in any electrical system. This guide has provided a thorough overview of the considerations involved, from initial selection to ongoing maintenance. Understanding the diverse applications, materials, and connection methods will empower you to make informed choices and build robust, reliable systems.