Electric tarp kits are revolutionizing construction and industrial sectors, offering a more efficient and safer alternative to manual systems. From streamlined setup to enhanced productivity, these innovative tools are reshaping the landscape of material handling. This guide delves into the intricacies of electric tarp kits, exploring their various applications, operational mechanics, and crucial safety considerations.
Understanding the diverse types, functionalities, and maintenance requirements is paramount for optimal performance. This in-depth analysis provides a comprehensive overview of the advantages and potential drawbacks, empowering users to make informed decisions based on specific project needs and industry requirements.
Overview of Electric Tarp Kits
Electric tarp kits are rapidly gaining traction across various industries, offering a more efficient and cost-effective alternative to traditional tarp-laying methods. These kits automate the process of covering and securing materials, saving significant labor time and improving overall project management. They’re particularly valuable in construction, logistics, and agriculture, where rapid tarp deployment is often crucial.Electric tarp kits represent a significant advancement in tarp handling.
Their automated operation reduces the need for manual labor, which in turn minimizes labor costs and the risk of human error, thereby increasing operational efficiency and safety. This automation is especially beneficial in large-scale projects and harsh weather conditions.
Types of Electric Tarp Kits
Electric tarp kits are available in diverse configurations to cater to varying project needs. Different sizes and materials are available to accommodate specific use cases, from small-scale temporary covers to large-scale, long-term protective solutions. Variations exist in the power source, control mechanisms, and even the tarp material itself.
Fundamental Components of an Electric Tarp Kit
A typical electric tarp kit comprises several key components. The power source, typically a battery or generator, provides the necessary energy. This energy drives the motor that actuates the tarp deployment mechanism, which might include motorized arms, winches, or pulleys. Safety features such as limit switches and emergency stop mechanisms are crucial to prevent accidents. A control panel or remote allows for precise operation and monitoring of the entire system.
Common Uses in Various Industries
Electric tarp kits find widespread applications in diverse industries. In construction, they’re used to cover materials and equipment during inclement weather, protecting them from rain, snow, and other elements. In logistics, these kits expedite the covering of goods during transportation, ensuring safe and secure delivery. Agricultural applications include covering crops or equipment to protect them from harsh weather or pests.
The kits are also valuable in event management, allowing for rapid and efficient setup and breakdown of temporary structures.
Comparative Analysis of Electric Tarp Kits
Kit Type | Size (approx.) | Features | Price Range (USD) |
---|---|---|---|
Basic Model | Small (10×10 ft) | Battery-powered, simple deployment mechanism, basic safety features. | $1,500 – $3,000 |
Mid-Range Model | Medium (20×20 ft) | Battery-powered, adjustable deployment speed, remote control, enhanced safety features. | $3,500 – $7,000 |
Commercial Grade | Large (40×40 ft+) | Generator-powered, high-capacity motor, multiple deployment points, advanced safety features, robust construction. | $8,000 – $20,000+ |
Note: Prices are estimates and can vary based on specific features, customization, and supplier.
Functionality and Operation
Electric tarp kits, a modern evolution of traditional tarp systems, offer significant advantages in speed, efficiency, and safety. These systems leverage electric motors and automated mechanisms to streamline the deployment process, eliminating the manual labor and potential injuries associated with traditional methods. Understanding the mechanics of these kits is crucial for effective utilization and maintenance.Electric tarp kits utilize a combination of electric motors, control systems, and automated mechanisms for precise and rapid tarp deployment.
These systems typically consist of a motorized winch, a control panel, and the tarp itself. The motors generate the force to reel out and retract the tarp, ensuring even tension and minimal effort. Control panels allow operators to precisely regulate the deployment speed and tension, maximizing efficiency and safety.
Mechanics of Operation
The core of an electric tarp kit’s operation revolves around a powerful electric motor coupled to a robust winch mechanism. This motor is the driving force behind the deployment and retraction of the tarp, which is often constructed from high-strength, weather-resistant materials. The motor’s power is regulated through a sophisticated control system, ensuring smooth and controlled movement. The system also includes sensors that monitor the tarp’s tension and position to maintain optimal deployment and prevent damage.
Setting Up and Deploying an Electric Tarp Kit
Proper setup is paramount for safe and efficient operation. Initial steps involve ensuring a secure anchoring system, which could involve stakes, anchors, or other suitable ground attachments. The kit’s control panel is then configured to establish the desired deployment parameters, such as speed and tension. The actual deployment process is typically initiated by a single button press on the control panel, activating the motorized winch to unfurl the tarp in a controlled manner.
Retraction is equally straightforward, reversing the process to quickly and safely fold the tarp. The tarp should be monitored during deployment to ensure there are no obstructions or tangles.
Comparison with Manual Systems
Manual tarp systems, relying on manual labor and potentially hazardous methods, often take considerably longer to deploy and retract. Electric tarp kits, in contrast, offer significant time savings, allowing for faster response times in emergency situations or other time-sensitive scenarios. Manual systems can expose workers to risks of physical strain and injury, whereas electric systems mitigate these risks, enhancing workplace safety.
Manual systems often lack the precision and control that electric systems provide.
Advantages and Disadvantages
Electric tarp kits offer several advantages over their manual counterparts. These include increased speed and efficiency, reduced risk of worker injury, and greater precision in deployment. However, the higher initial cost of an electric tarp kit is a notable disadvantage. Maintenance requirements can also be more complex and require specialized personnel or tools. Furthermore, power outages can disrupt operation, requiring backup power solutions.
Maintenance for Optimal Performance
Regular maintenance is crucial for ensuring the longevity and optimal performance of an electric tarp kit. This involves routine inspections of the winch, motor, control panel, and associated components. Lubrication of moving parts is essential to prevent wear and tear. Regular cleaning of the tarp and its associated hardware is critical for maintaining its durability and preventing damage from environmental factors.
Consult the manufacturer’s recommendations for specific maintenance procedures. Furthermore, adhering to manufacturer-recommended maintenance schedules ensures consistent performance and extends the lifespan of the system.
Materials and Construction
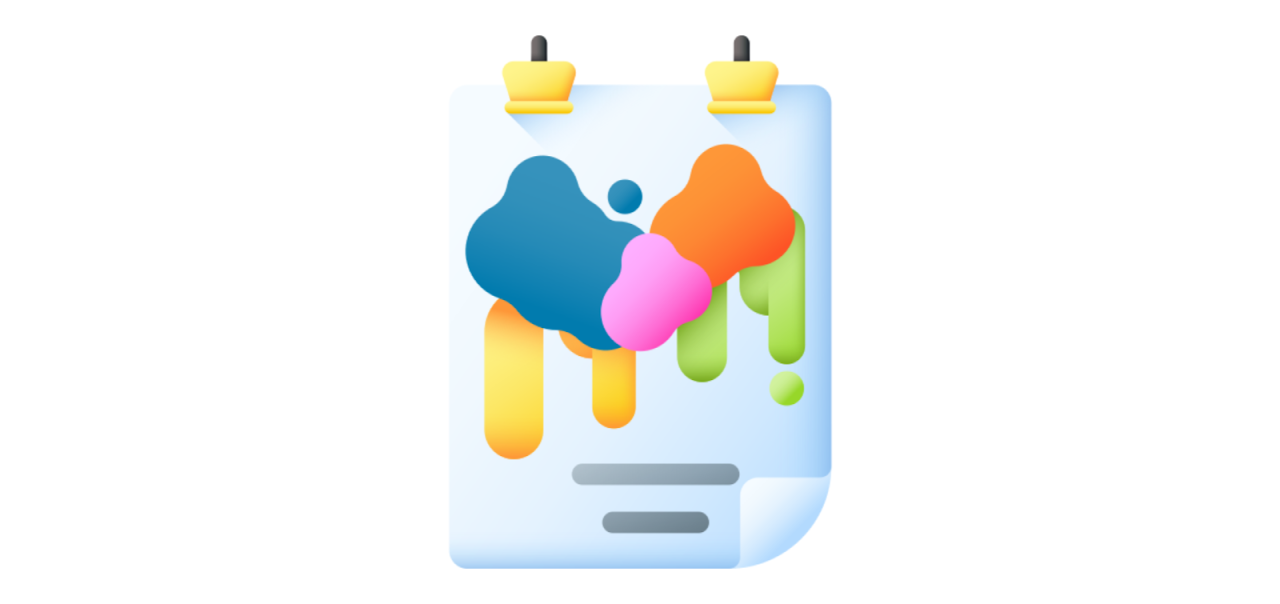
Electric tarp kits, crucial for temporary structures in diverse settings, demand robust materials and meticulous construction. The durability and weather resistance of these kits are paramount, ensuring longevity and functionality across various climates and conditions. Understanding the specific materials and construction methods employed is essential for evaluating the overall performance and safety of these systems.
Common Materials
The construction of electric tarp kits typically involves a combination of high-strength, weather-resistant materials. Polyester and vinyl tarps are frequently used due to their inherent water resistance and tensile strength. These materials are often reinforced with a variety of backing materials, like coated fabrics or fiberglass mesh, to further enhance their durability and tear resistance. Frame components, often constructed from aluminum or steel, provide structural integrity and are treated for corrosion resistance.
Electrical components, including wires, connectors, and lighting fixtures, are chosen for their reliability and safety ratings.
Durability and Weather Resistance
The durability of electric tarp kits is directly linked to the quality and properties of the materials used. High-quality polyester tarps, for instance, exhibit exceptional resistance to tearing and UV degradation, extending the lifespan of the structure. Vinyl tarps, often coated with a polyurethane layer, provide excellent water resistance, protecting the underlying structure from rain, snow, and other forms of precipitation.
The selection of appropriate materials ensures the kit can withstand expected environmental conditions, such as strong winds, heavy rainfall, and temperature fluctuations. Frame materials, such as aluminum alloys, are known for their corrosion resistance and strength-to-weight ratio, contributing to the longevity of the entire structure.
Construction Methods
Electric tarp kits are assembled using a variety of techniques, each designed to maximize strength and stability. The frames are often pre-assembled and then connected to the tarp using specialized fasteners and attachments. Careful attention is paid to ensuring proper tensioning of the tarp, avoiding wrinkles and ensuring a watertight seal. The electrical components are integrated into the structure following established safety protocols and codes, with thorough grounding and insulation procedures.
Seams and connections are carefully sealed to prevent water ingress and maintain structural integrity.
Safety Features
Safety is paramount in the design and construction of electric tarp kits. These features include robust grounding systems for electrical components, ensuring that any electrical fault is safely dissipated. Appropriate insulation is applied to all electrical wiring and connections, mitigating the risk of shock hazards. High-quality fasteners and attachment points are chosen to maintain structural integrity and prevent failures under load.
Clear labeling of electrical components and instructions for safe operation are included for user safety.
Comparative Analysis of Tarp Materials
Material | Pros | Cons |
---|---|---|
Polyester | High tensile strength, good UV resistance, relatively affordable | May not be as water-resistant as vinyl, can be more prone to tearing in high winds. |
Vinyl | Excellent water resistance, good durability, high tear resistance | Can be more expensive than polyester, can become brittle in extreme cold temperatures. |
Fiberglass Reinforced | Superior tensile strength and tear resistance, good dimensional stability | Heavier than polyester or vinyl, can be more expensive. |
Safety Considerations
Electric tarp kits, while offering efficiency in various applications, necessitate meticulous adherence to safety protocols. Neglecting these precautions can lead to severe injuries and equipment damage. This section details critical safety considerations, procedures, and potential hazards associated with electric tarp kits.
Essential Safety Precautions
Proper setup, operation, and maintenance of electric tarp kits are paramount to prevent accidents. Failure to follow these procedures can result in electrocution, equipment malfunction, or physical injury. Strict adherence to safety guidelines is crucial for personnel and surrounding environments.
Setup Safety Procedures
Before initiating setup, a thorough inspection of the kit’s components is essential. Damaged cables, frayed wires, or loose connections must be immediately addressed. Ensure the working area is clear of obstructions and personnel. The ground must be level and free from moisture or debris. Use appropriate protective equipment, including insulated gloves and safety glasses, throughout the setup process.
Grounding the equipment to a dedicated electrical source is vital for preventing electrical shocks.
Operational Safety Procedures
During operation, maintain a safe distance from the equipment. Avoid contact with exposed wires or moving parts. Regular checks for any signs of damage or malfunction are essential. Do not overload the system. Never operate the kit in adverse weather conditions, such as heavy rain or strong winds.
If any unusual sounds or vibrations are detected, immediately cease operation and assess the situation. Proper training and familiarity with the kit’s operation are crucial for personnel handling the equipment.
Maintenance Safety Procedures
Regular maintenance is vital for the longevity and safe operation of electric tarp kits. Inspect the cables, motors, and connections for any signs of wear or damage. Lubricate moving parts as per the manufacturer’s recommendations. Never attempt repairs unless adequately trained and equipped. Ensure that all maintenance activities are conducted with the equipment turned off and the power source disconnected.
Potential Hazards
Electric tarp kits pose several potential hazards, including electrocution, entanglement, and equipment malfunctions. Electrocution risk is heightened if the kit’s grounding system is faulty or compromised. Entanglement with cords or moving parts can lead to injuries. Malfunctioning equipment can cause significant damage to the tarp or the structure being covered. Proper maintenance and training can significantly mitigate these hazards.
Emergency Procedures
In case of malfunctions or accidents, immediate action is critical. If an electrical shock occurs, disconnect the power source immediately. Seek medical attention for injuries. Document the incident for future reference and to facilitate preventative measures. Report any near misses or incidents to the appropriate personnel for analysis and corrective actions.
Knowing the location of emergency shut-off switches is crucial.
Safety Checklist
- Thorough inspection of the kit before each use.
- Wearing appropriate personal protective equipment (PPE).
- Ensuring a safe and clear working area.
- Checking the grounding system for proper functionality.
- Following the manufacturer’s instructions for operation and maintenance.
- Having a well-defined emergency plan and procedure.
- Regular maintenance and inspection to prevent potential failures.
Applications and Industries
Electric tarp kits are revolutionizing various industries, offering streamlined and efficient solutions for covering and protecting goods. Their versatility, coupled with reduced labor costs and environmental benefits, positions them as a valuable asset across diverse sectors. From construction sites to agricultural fields, these kits are transforming logistical processes.These automated tarp systems offer substantial advantages in terms of speed and efficiency.
By reducing manual labor and the associated risks, they enhance safety and productivity. The standardized design and readily available components contribute to faster deployment and streamlined maintenance, further enhancing their appeal to businesses seeking operational improvements.
Construction Industry
Electric tarp kits excel in the construction sector, where rapid and efficient site coverage is critical. Their use minimizes downtime and allows for continuous operations. Specific applications include protecting exposed materials from inclement weather, securing equipment, and safeguarding construction sites from theft. The reduction in labor costs is a significant advantage, especially on large-scale projects. The unique challenge in this industry revolves around the diverse and often dynamic construction environments.
Varying site conditions, equipment configurations, and the need for flexibility in tarp deployment require specialized kit designs and adaptable features.
Agriculture
Electric tarp kits are increasingly adopted in agriculture for various purposes, such as protecting harvested crops from rain and other environmental elements. This helps to maintain the quality and condition of the goods. Examples include covering freshly harvested produce during transportation, sheltering livestock from adverse weather, and protecting stored grains from pests and moisture. The benefits include enhanced crop preservation and reduced spoilage, leading to higher yields and lower losses.
Challenges arise from the unpredictable nature of weather patterns and the necessity of adapting tarp sizes and configurations to diverse agricultural equipment.
Logistics and Warehousing
In logistics and warehousing, electric tarp kits provide a streamlined solution for covering and securing cargo during transportation and storage. This ensures that the goods remain protected from the elements. Specific applications include protecting goods from rain, snow, or direct sunlight, safeguarding inventory during loading and unloading operations, and covering goods during transit. The benefits include reduced damage to goods, enhanced security, and faster turnaround times.
A major challenge in this sector is the varying sizes and types of cargo handled, requiring a diverse range of tarp kits and adaptable deployment systems.
Table: Industries, Applications, and Benefits of Electric Tarp Kits
Industry | Applications | Benefits |
---|---|---|
Construction | Protecting materials, securing equipment, safeguarding sites | Minimized downtime, continuous operations, reduced labor costs |
Agriculture | Protecting crops, sheltering livestock, protecting stored grains | Enhanced crop preservation, reduced spoilage, higher yields |
Logistics & Warehousing | Protecting cargo during transport and storage, securing inventory | Reduced damage to goods, enhanced security, faster turnaround times |
Maintenance and Troubleshooting
Proactive maintenance is crucial for the longevity and optimal performance of electric tarp kits. Regular checks and timely repairs prevent costly breakdowns and ensure the system operates reliably under various conditions. This section details a comprehensive maintenance schedule, troubleshooting steps, and component-specific considerations to maintain peak efficiency.
Routine Maintenance Schedule
A well-defined maintenance schedule is essential for preventing issues and maximizing the life of the electric tarp kit. This schedule should be tailored to the specific operating conditions and frequency of use. The following table provides a recommended maintenance schedule.
Frequency | Tasks |
---|---|
Weekly | Visual inspection of all components, including the motor, drive belts, pulleys, and tarp tensioning mechanisms. Check for signs of wear, damage, or unusual noises. Lubricate moving parts as needed. |
Monthly | Thorough cleaning of the entire system, removing dirt, debris, and accumulated moisture. Inspect electrical connections for corrosion or damage. Test all safety features, such as emergency stops and overload protection. |
Quarterly | Detailed inspection of the tarp itself, checking for tears, holes, or signs of wear and tear. Ensure proper tensioning and adjust as needed. Verify all wiring connections for security and proper functioning. |
Annually | Professional inspection and servicing of the electrical system by a qualified technician. This includes motor diagnostics, belt replacement (if necessary), and general component checks. |
Routine Maintenance Procedures
Following these steps during routine maintenance will help prevent major issues.
- Visual Inspection: Carefully examine all components for signs of damage, wear, or unusual noises. Look for frayed belts, loose connections, or any evidence of moisture damage. Note any discrepancies for later action.
- Lubrication: Lubricate moving parts, such as pulleys and gears, with the appropriate lubricant specified by the manufacturer. Excessive or insufficient lubrication can lead to premature wear and tear.
- Cleaning: Thoroughly clean the entire system, removing dirt, dust, and debris. This prevents the buildup of contaminants that can affect performance and shorten the life of the equipment.
- Electrical Safety Checks: Inspect all electrical connections for corrosion, damage, or loose connections. Ensure that all safety devices, such as circuit breakers and emergency stops, function correctly. Any electrical issues should be addressed by a qualified electrician immediately.
Troubleshooting Malfunctions
Troubleshooting malfunctions can be simplified by a systematic approach. Early detection and intervention can minimize downtime and potential damage.
- Identify the Issue: The first step in troubleshooting is to pinpoint the specific problem. Note any unusual noises, vibrations, or performance issues. Is the tarp not deploying? Is the motor making strange sounds? These are vital clues.
- Check for Obstructions: Ensure there are no obstructions in the path of the tarp or the moving parts. Objects caught in the system can cause damage and malfunctions.
- Verify Power Supply: Confirm the power supply is adequate and functioning correctly. A faulty electrical connection can lead to a variety of problems.
- Component Replacement: If the problem persists after checking basic components, consider replacing worn-out or damaged parts. This may include drive belts, pulleys, or the motor itself.
Identifying and Addressing Common Component Issues
Addressing component issues proactively prevents more serious problems. Recognizing common issues and understanding their remedies is critical.
- Motor Problems: Unusual noises, overheating, or failure to start are signs of potential motor problems. A qualified technician should inspect and diagnose the motor for faults.
- Belt Wear: Frayed or cracked belts can lead to reduced efficiency and potential system failures. Replace worn belts promptly to maintain optimal performance. The manufacturer’s specifications should guide the replacement process.
- Electrical Issues: Faulty wiring or loose connections can lead to malfunctions or safety hazards. A professional electrician should be consulted for diagnosing and resolving electrical problems.
Importance of Regular Inspections
Regular inspections are critical for preventing major failures and ensuring safe operation. A comprehensive inspection schedule helps identify potential issues before they escalate into costly repairs or safety hazards. Predictive maintenance based on regular inspections minimizes unplanned downtime and enhances the longevity of the electric tarp kit.
Cost and Price Analysis
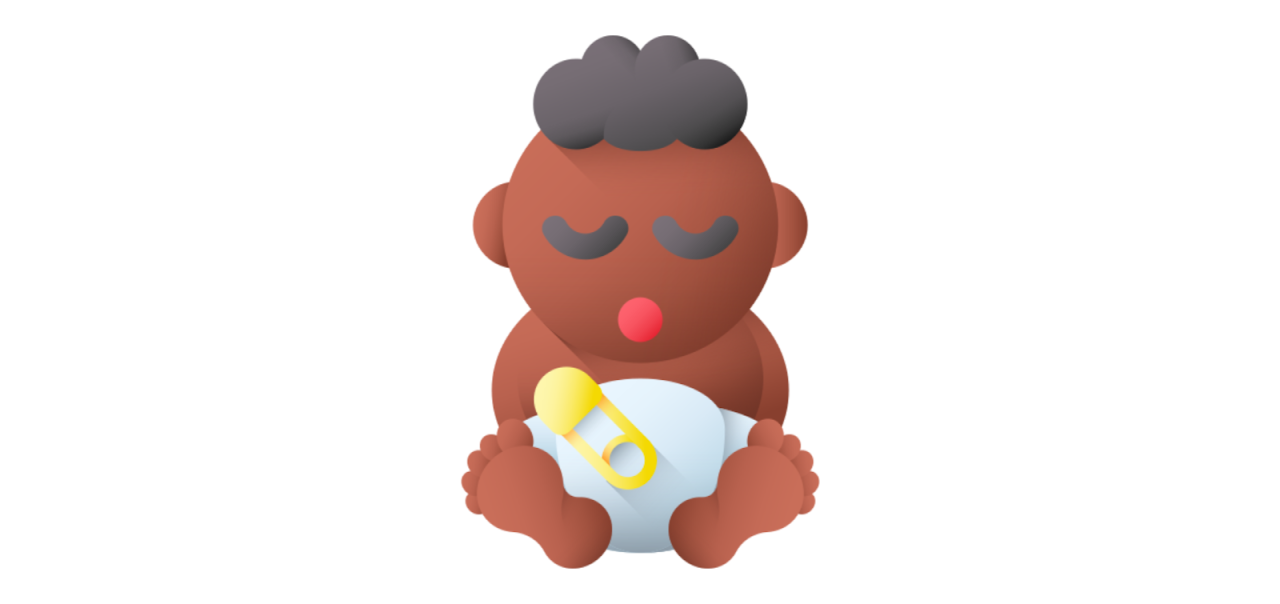
Electric tarp kits, while offering significant operational advantages, come with a spectrum of costs that vary based on features, specifications, and the overall operational context. Understanding these factors is crucial for businesses seeking to maximize return on investment (ROI) and optimize their material handling processes.The price of an electric tarp kit is not simply a function of the machine itself.
Hidden costs, such as maintenance, potential downtime, and accessory needs, contribute substantially to the total cost of ownership. A comprehensive evaluation considers these indirect costs alongside the initial purchase price.
Cost Factors
Several factors contribute to the overall cost of an electric tarp kit. These include the machine’s power requirements, the quality and type of materials used in its construction, the complexity of its functionalities, and the availability of various accessories. A more sophisticated system with advanced features, such as automated controls or multiple tarp handling capabilities, will generally command a higher price point.
- Initial Purchase Price: This represents the upfront cost of the electric tarp kit itself. Variations in this price are driven by the factors mentioned above, including the sophistication of the machine’s functionalities and the quality of its components. A basic model will likely be more affordable than a high-end model with advanced features like remote operation or integrated weighing systems.
- Accessories: The cost of accessories like extra tarps, extension arms, or safety features can add significantly to the overall expense. Businesses should carefully assess their specific needs to avoid unnecessary costs associated with accessories they don’t require. For example, a company that only handles light loads may not need the advanced safety features of a heavy-duty model.
- Installation and Setup Costs: While often overlooked, installation and setup costs can range depending on the complexity of the installation process. These costs can include labor, specialized tools, and any required modifications to existing infrastructure. Businesses should factor in these costs to determine the total investment needed.
- Maintenance and Repair Costs: The long-term maintenance and repair costs associated with an electric tarp kit should be considered. Regular maintenance can prevent costly repairs, while higher-quality components will generally lead to lower maintenance expenses over time. The type of maintenance and repair costs will vary based on the specific model of the electric tarp kit.
- Energy Costs: Electric tarp kits consume energy. Businesses should consider the cost of electricity and potential fluctuations in energy rates to accurately estimate the long-term energy costs. The energy consumption will vary based on the size and power requirements of the electric tarp kit.
Price Comparison
The cost of electric tarp kits varies significantly depending on their features and specifications. A direct comparison requires considering not only the base price but also the included accessories. A thorough assessment requires a careful comparison of different models.
Model | Base Price | Accessories (e.g., Extra Tarps, Extension Arms) | Total Price |
---|---|---|---|
Model A (Basic) | $5,000 | $1,000 | $6,000 |
Model B (Mid-Range) | $8,000 | $1,500 | $9,500 |
Model C (High-End) | $12,000 | $2,500 | $14,500 |
Return on Investment (ROI)
The ROI of an electric tarp kit depends on factors such as labor savings, reduced material handling costs, and improved efficiency. Companies in industries with high material handling volumes are likely to see a faster ROI. A careful assessment of these factors will determine the overall return on investment. For instance, a warehouse handling thousands of packages daily could potentially see a significant ROI from the automation provided by an electric tarp kit.
Environmental Impact
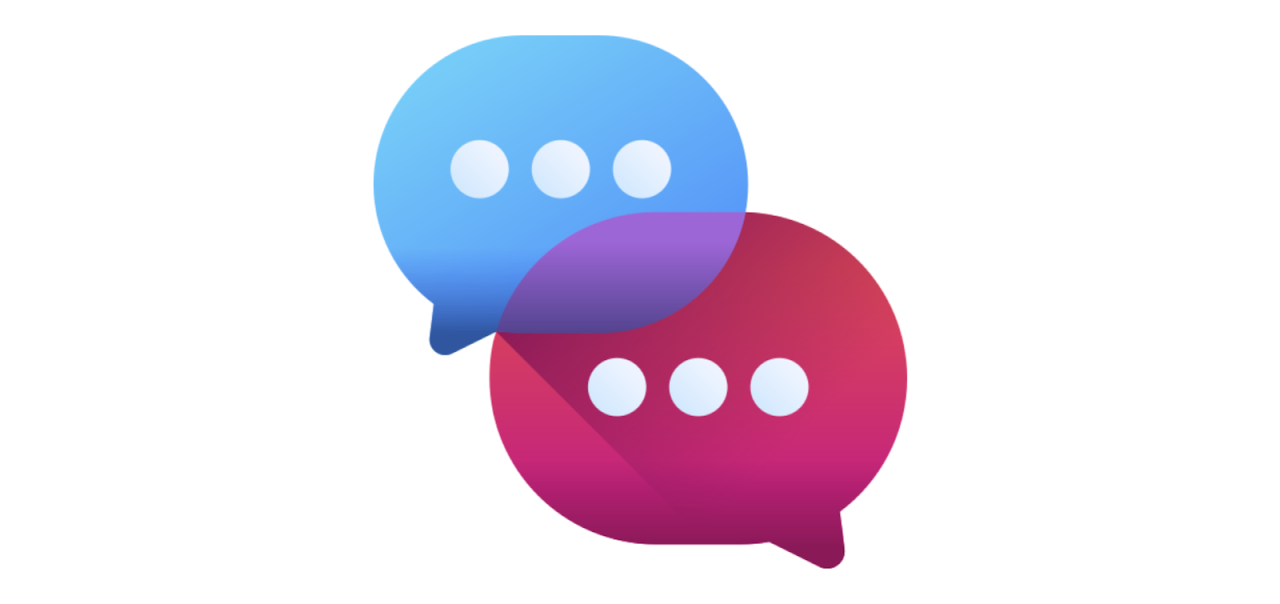
Electric tarp kits, while offering significant operational advantages, introduce a nuanced environmental consideration. Their adoption necessitates a comprehensive evaluation of their lifecycle impact, from material sourcing to disposal. A thorough understanding of these factors is crucial for informed decision-making and sustainable practices in the construction and industrial sectors.Electric tarp kits, in comparison to manual methods, can present both positive and negative environmental consequences.
A detailed analysis of materials, energy consumption, and disposal procedures is essential to fully assess their environmental footprint.
Material Composition and Environmental Impact
The environmental impact of electric tarp kits is intricately linked to the materials used in their construction. The primary materials employed in these kits often include high-strength polymers, conductive wires, and motor components. The environmental impact of each material varies significantly. For instance, some polymers are derived from petroleum-based sources, contributing to carbon emissions during production and potentially posing plastic waste challenges at the end of the kit’s lifespan.
Conversely, recycled polymers or bio-based alternatives can offer a more sustainable solution. The specific sourcing and composition of materials should be scrutinized to determine the overall environmental impact.
Energy Consumption Analysis
The energy consumption of electric tarp kits varies significantly based on factors such as the size of the tarp, the operational mode, and the efficiency of the motor. Manufacturers often provide energy consumption data in kilowatt-hours per operation or per hour of use. This data allows for comparisons between different models and estimations of overall energy consumption during a project.
Electric tarp kits can offer substantial energy savings compared to manual systems, especially for large-scale operations where human labor is intensive. However, the electricity used to power the kits originates from various sources, each with its own environmental impact. This impact must be considered alongside the energy savings achieved by using the kits.
Potential Environmental Benefits
Electric tarp kits can offer significant environmental benefits over manual alternatives. These benefits arise from reduced reliance on human labor, minimizing the physical strain on workers and the associated health risks. The reduced need for repetitive manual lifting and hauling can contribute to a safer working environment, thus reducing the likelihood of workplace injuries. Moreover, the automated process can increase efficiency and productivity, potentially shortening project timelines.
The reduction in labor costs can be offset by the operational savings, ultimately leading to a more sustainable approach to project completion.
Disposal Procedures
Proper disposal of electric tarp kits is crucial to minimize environmental damage. Kits should be disassembled into component parts, separating recyclable materials such as polymers and metals. Electronic components should be disposed of according to local regulations, ensuring compliance with hazardous waste disposal guidelines. The disposal process should be standardized and transparent to facilitate proper handling and recycling of the materials.
This ensures that the environmental impact is minimized at the end of the kit’s lifespan.
Accessories and Options
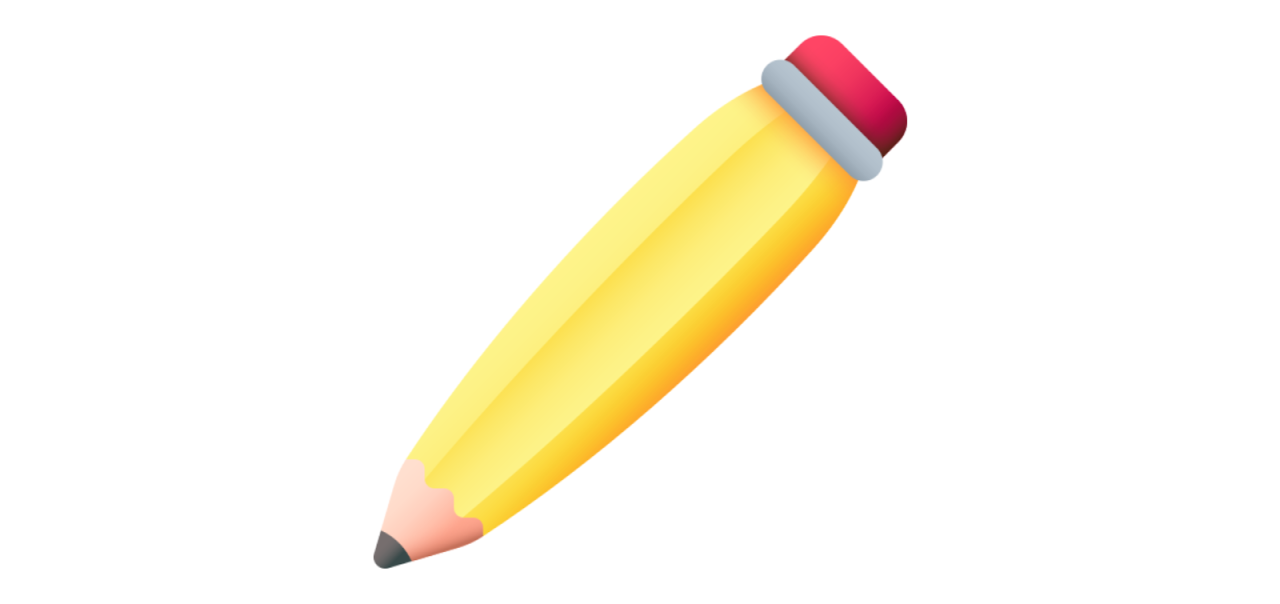
Electric tarp kits, while fundamentally capable of automated tarp deployment, can be further customized and enhanced with a variety of accessories. These additions often cater to specific operational needs, increasing efficiency and safety, especially in challenging environments. Tailoring the kit to the job at hand maximizes its potential.
Available Accessories
Electric tarp kits benefit from a range of accessories, each designed to improve functionality, safety, and overall operational efficiency. These accessories address specific challenges encountered during deployment and maintenance, often increasing operational efficiency in diverse industrial settings.
- Remote Control Units: Remote control units offer enhanced maneuverability and safety, allowing operators to control the tarp deployment from a safe distance. This is crucial in high-risk environments or when operating in confined spaces. Improved safety protocols reduce the risk of injury and downtime, making operations smoother.
- Wind Sensors and Automatic Shut-off Mechanisms: Integration of wind sensors and automatic shut-off mechanisms ensures that the tarp deployment process remains safe and effective. These safeguards are especially vital in windy conditions, preventing potential damage to the tarp or equipment. The addition of such sensors ensures the tarp deployment process remains efficient and controlled.
- Lighting Systems: Lighting systems are critical for safe operation in low-light conditions. These accessories significantly enhance visibility, allowing for safe and effective tarp deployment in darkness or poor visibility. The implementation of lighting systems minimizes the risk of accidents and ensures smooth operation in various environments.
- Support Structures and Anchoring Systems: Additional support structures and anchoring systems improve the stability and security of the deployed tarp. These additions are crucial in uneven or unstable terrain, ensuring that the tarp remains securely in place during operation. The implementation of robust anchoring systems ensures the safety and efficiency of the tarp system.
- Maintenance Kits and Spare Parts: A dedicated maintenance kit, including spare parts for critical components, reduces downtime and ensures the longevity of the electric tarp kit. This proactive approach to maintenance significantly enhances operational reliability and minimizes unexpected interruptions. A comprehensive maintenance kit ensures that the electric tarp kit remains in peak operational condition.
Compatibility and Enhancements
Accessories for electric tarp kits are often designed with specific models in mind. Compatibility and functionality are paramount in optimizing the performance of the entire system.
Accessory | Function | Compatibility (Example Models) |
---|---|---|
Remote Control Unit | Enhanced control and safety from a distance. | Model A, Model B (Advanced), Model C (Premium) |
Wind Sensor/Automatic Shut-off | Automatic safety response to high winds. | Model A, Model B (Advanced), Model C (Premium) |
Lighting System | Improved visibility for nighttime operations. | Model A, Model B (Advanced), Model C (Premium) |
Support Structures | Increased stability and security for tarp deployment. | Model A, Model B (Advanced) |
Maintenance Kit | Proactive maintenance to extend equipment lifespan. | All Models |
Accessories are designed to enhance the functionality and safety of electric tarp kits, optimizing their performance in various applications.
Outcome Summary
In conclusion, electric tarp kits represent a significant advancement in material handling. Their efficiency, safety features, and diverse applications across various industries make them a compelling investment. However, careful consideration of maintenance, safety protocols, and environmental impact is crucial for maximizing the return on investment and minimizing potential risks. This comprehensive guide equips users with the knowledge necessary to navigate the complexities of electric tarp kits, ensuring optimal performance and safety throughout their lifespan.